The Future of Manufacturing Is Here
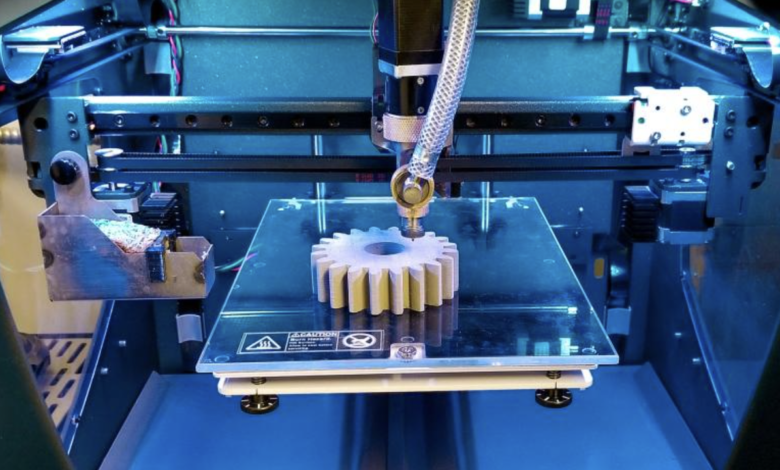
The world of manufacturing is changing fast. 3D printing, once a niche technology reserved for prototypes and hobbyists, is now a full-scale production solution for industries like automotive, aerospace, healthcare, and consumer goods. As demand for high-quality, cost-effective, and sustainable manufacturing grows, HP’s Multi Jet Fusion technology is leading the way with a new generation of 3D printing materials that are stronger, smarter, and more sustainable than ever.
But why are materials so important? The reality is that even the most advanced 3D printers can only go so far if the materials they use don’t meet the demands of modern engineering. HP understands this, and that’s why they’ve developed a versatile portfolio of high-performance thermoplastics designed to push the boundaries of what’s possible in additive manufacturing.
Why HP’s 3D Printing Materials Are a Game-Changer
When you think of 3D printing, you might imagine plastic parts that are weak, brittle, or rough around the edges. That’s no longer the case. HP has engineered materials that rival (and in some cases outperform) traditionally manufactured parts. These materials offer:
✅ High strength and durability – Ideal for industrial-grade parts and functional prototypes.
✅ Excellent chemical and heat resistance – Ensuring reliability in harsh environments.
✅ Sustainability – Many HP materials have high reusability rates, reducing waste and cost.
✅ Versatility – Whether you need rigid, flexible, impact-resistant, or ultra-smooth parts, there’s an HP material for the job.
Let’s take a look at some of the most exciting materials HP has developed and how they’re changing the game in 3D-printed manufacturing.
PA 12: The Industry Workhorse
What is it?
Polyamide 12 (PA 12) is one of the most widely used materials in industrial 3D printing because it balances strength, cost-efficiency, and precision. It’s ideal for functional prototypes and end-use parts that require durability and dimensional accuracy.
Why it’s special
PA 12 is a high-density thermoplastic that resists chemicals, oils, and moisture, making it perfect for automotive, aerospace, and consumer product applications. Plus, it offers an industry-leading powder reusability rate of up to 80%, reducing material waste and lowering production costs.
Common uses
- Housings and enclosures for electronic devices
- Watertight parts for fluid handling systems
- Automotive and aerospace components that require lightweight strength
PA 11: Stronger, More Flexible, and Eco-Friendly
What is it?
PA 11 is similar to PA 12 but with one major advantage: it’s made from renewable castor oil, making it a more sustainable choice. It’s also tougher and more flexible, making it great for parts that need impact resistance and high elongation-at-break (the ability to stretch without snapping).
Why it’s special
This material reduces its carbon footprint by 46% compared to petroleum-based plastics. Plus, it’s biocompatible, meaning it can be used safely for medical applications like prosthetics and braces.
Common uses
- Sports equipment like protective gear and insoles
- Snap fits and living hinges that require flexibility
- Medical devices and prosthetics
PA 12 S: The Go-To for Smooth, High-Detail Parts
What is it?
PA 12 S is a specialized material developed for premium surface finishes. It produces parts that come out of the printer up to 70% smoother, making it perfect for consumer-facing applications where aesthetics matter.
Why it’s special
It’s designed to minimize post-processing, meaning you spend less time refining parts after printing. It also has high dimensional accuracy, so even the most intricate designs come out clean and crisp.
Common uses
- Dental molds and aligners
- Consumer electronics casings
- Fashion and wearables
PA 12 Glass Beads: Extra Stiffness for High-Precision Parts
What is it?
PA 12 Glass Beads is a glass bead-filled polyamide designed for parts that need high stiffness and dimensional stability. This means less warping, more precision, and increased rigidity.
Why it’s special
By adding 40% glass beads, HP has created a material that resists deformation under stress and heat, making it ideal for fixtures, jigs, and tooling. It’s also highly recyclable, with up to 70% of powder being reusable in future prints.
Common uses
- Aerospace and automotive housings
- Manufacturing tools and fixtures
- Industrial machine components
Polypropylene (PP): The Most Cost-Effective 3D Printing Material
What is it?
PP (Polypropylene) is a lightweight, chemically resistant, and highly durable thermoplastic. It’s one of the most widely used plastics in traditional manufacturing, and HP has optimized it for 3D printing.
Why it’s special
PP is the lowest-cost HP 3D printing material, with an unbeatable 90% reusability rate. It’s also weldable, meaning it can be easily combined with traditionally manufactured PP parts.
Common uses
- Fluid storage containers and piping
- Automotive interiors
- Medical-grade applications
Flexible TPA: The Ultimate for Soft, Bouncy, Lightweight Parts
What is it?
TPA (Thermoplastic Polyamide-Elastomer) is a flexible, lightweight material that is ideal for parts requiring high elasticity and rebound resilience.
Why it’s special
TPA maintains excellent shape memory, meaning it bends and flexes but always returns to its original form. It’s perfect for wearables, robotics, and soft-touch applications.
Common uses
- Winter sports equipment
- Flexible robotic grippers
- Medical wearables
Why This Matters for Businesses and Manufacturers
The power of HP’s Jet Fusion materials goes beyond just making cool parts. It’s about:
✔ Lowering costs – More efficient powder reusability means less waste and lower expenses.
✔ Faster production – HP’s materials are designed for high-speed, high-quality manufacturing.
✔ Stronger, better parts – These thermoplastics offer superior mechanical properties compared to many traditional materials.
✔ Sustainability – With materials like bio-based PA 11 and high-reusability PP, HP is making 3D printing more eco-friendly.
Ready to Take Advantage of HP Jet Fusion Materials?
If you’re looking to integrate HP’s cutting-edge materials into your manufacturing process, RapidMade can help. We specialize in high-performance 3D printing and advanced manufacturing solutions, helping businesses innovate, cut costs, and scale production.
🚀 Start your journey into the future of digital manufacturing today.
🔹 Visit RapidMade.com to learn more!