Understanding 5-Axis Machined Parts
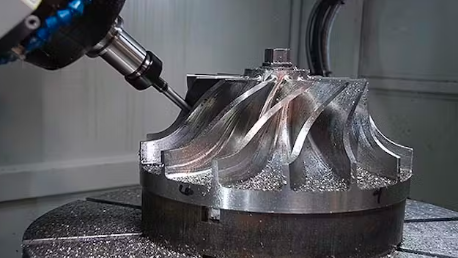
Introduction to 5-Axis Machining
5-axis machining is an advanced CNC (Computer Numerical Control) method that enables the cutting tool and workpiece to move simultaneously across five axes: X, Y, Z, A, and B. While the X, Y, and Z axes control the linear movement of the tool in three-dimensional space, the A and B axes add rotational movement, providing greater flexibility and precision. This allows manufacturers to create highly intricate and detailed parts that are difficult or impossible to produce with conventional methods. Parts machined using 5-axis technology are essential in industries requiring high precision and complexity, such as aerospace, automotive, and medical device production.
Benefits of 5-Axis Machined Parts
- Precision and Accuracy
A significant advantage of 5-axis machining is the ability to achieve extreme precision and accuracy. The added rotational axes facilitate the creation of complex shapes in a single setup, which minimizes errors and ensures the final product meets the required tolerances. This is particularly important in fields like aerospace, where parts must fit together flawlessly and perform reliably. - Reduced Setup Time
Traditional machining methods often require multiple setups to machine parts with complex geometries, increasing time and labor costs. With 5-axis machining, the workpiece can be machined from all angles without needing to reposition it, cutting down on setup times and enhancing production efficiency. - Complex Geometries
The ability to machine complex shapes is one of the standout features of 5-axis milling. This is invaluable for industries like aerospace and medical devices, where intricate design details are essential. - Improved Surface Finish
5-axis machining allows for better tool positioning, which results in smoother surface finishes. The ability to choose optimal angles for cutting minimizes tool wear and reduces the force required for machining, which translates into fewer post-machining processes like polishing or grinding. This is particularly advantageous for industries where surface quality is critical, such as in the manufacture of medical implants or high-performance automotive components. - Efficient Material Removal
The versatility of 5-axis machining allows for optimized cutting paths, enabling faster material removal and reducing the risk of tool damage. This is particularly useful for machining difficult materials like titanium or hardened steel, allowing for faster and more cost-efficient production cycles.
Industries That Use 5-Axis Machined Parts
- Aerospace
The aerospace sector relies on 5-axis machining to produce highly precise and complex components, such as turbine blades and engine parts, which require tight tolerances and high performance. The ability to machine intricate shapes ensures that parts meet the demanding standards of this industry. - Medical Devices
Precision is critical in the medical device industry, where parts like surgical instruments and implants must be manufactured to exact specifications. 5-axis machining allows for the production of custom implants and complex surgical tools with high precision and reliability, ensuring that they function safely and effectively. - Automotive
The automotive industry uses 5-axis machining for producing high-performance components, such as engine parts, transmission systems, and other intricate parts that require complex geometries. The technology enables the design of innovative and efficient vehicles, including high-performance and electric models. - Tool and Die Making
Tool and die makers use 5-axis machining to create precision molds, dies, and fixtures with complex shapes and features. The ability to machine these parts in a single setup results in better accuracy and improved quality for mass-produced components. - Defense and Military
In defense and military applications, 5-axis machining is essential for creating highly specialized and durable components, including missile parts, military vehicle components, and weapons systems. The precision and ability to create complex shapes make 5-axis machining ideal for meeting the high standards of accuracy and reliability required in this sector.
How 5-Axis Machining Works
Machine Setup
The process starts by selecting the appropriate material 5 axis machined parts and setting up the 5-axis machine. The workpiece is typically placed on a rotary table that enables rotation along multiple axes while the cutting tool moves. Once the program is loaded into the machine’s control system, the machine is calibrated to ensure precision during the machining process.
Read also: Revolutionizing Data Protection with Inline Memory Encryption Technology
- Cutting Process
The cutting tool moves along the X, Y, and Z axes to machine the workpiece, while the A and B axes rotate the part to ensure the tool can approach it from all necessary angles. High-speed cutting tools and advanced cooling techniques are employed to improve machining efficiency and reduce tool wear. - Final Product
After machining, the part undergoes quality checks to verify that it meets the required dimensions and tolerances. Techniques such as coordinate measuring machines (CMM) are used to inspect the part. Post-processing operations, including polishing or coating, may be performed to enhance surface finish and functionality.
Challenges in Producing 5-Axis Machined Parts
- Complex Programming
One challenge in 5-axis machining is the complexity of the programming required to control the machine. Unlike 3-axis machines, where the tool paths are relatively simple, 5-axis machines require advanced programming to manage the movements of both the tool and the workpiece. This necessitates skilled operators who are familiar with both the machinery and the specialized software used for programming. - High Costs
The advanced equipment required for 5-axis machining comes with high upfront costs, and the maintenance of such machines can be expensive. However, the benefits in terms of precision, reduced setup time, and faster production can justify the higher initial investment in the long term.
Conclusion
5-axis machining is an essential process in modern manufacturing, offering significant advantages such as precision, efficiency, and the ability to create complex geometries. This advanced technology is indispensable in industries like aerospace, automotive, medical devices, and defense, where high-quality, high-performance components are required. Despite the initial costs and complexity, the long-term benefits of 5-axis machining in terms of speed, accuracy, and material versatility make it an invaluable tool for companies that demand the highest level of precision in their products.