What Does Medical Device Plastic Molding Mean?
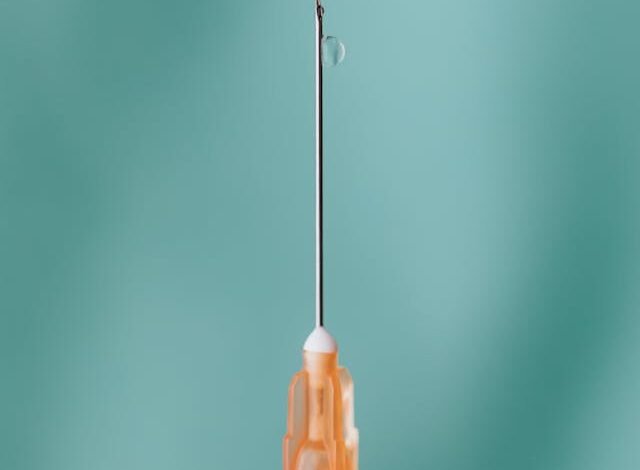
Medical device plastic Molding is a manufacturing process that involves shaping plastic materials into intricate components used in medical devices. This process is crucial in the production of various medical tools and equipment, ranging from syringes and catheters to complex surgical instruments and implantable devices.
Introduction to Medical Device Plastic Molding
In the realm of medical device manufacturing, precision and consistency are paramount. Medical device plastic Molding addresses these needs by providing a reliable method for producing high-quality components with tight tolerances.
Importance of Medical Device Plastic Molding
Precision and Consistency
One of the primary advantages of medical device plastic Molding is its ability to create intricate parts with precise dimensions repeatedly. This precision is essential for ensuring the functionality and reliability of medical devices.
Cost-effectiveness
Medical device plastic Molding offers cost advantages over traditional manufacturing methods, such as machining or casting. The ability to mass-produce components with minimal material waste makes it an economically viable option for large-scale production.
Types of Medical Device Plastic Molding
Injection Molding
Medical Injection Molding is the most common method used in medical device manufacturing. It involves injecting molten plastic material into a mould cavity, where it cools and solidifies to form the desired shape.
Blow Molding
Blow Molding is another technique employed in the production of hollow plastic parts, such as bottles and containers. In medical device manufacturing, this process is utilized for creating items like IV bags and tubing.
Compression Molding
Compression Molding is suitable for producing large, solid parts with complex geometries. It involves placing a preheated plastic material into a heated mould cavity, followed by applying pressure to shape the material.
Materials Used in Medical Device Plastic Molding
Thermoplastics
Thermoplastics are the most commonly used materials in medical device plastic Molding due to their versatility, durability, and biocompatibility. Popular thermoplastics include polyethylene, polypropylene, and polycarbonate.
Thermosets
Thermoset plastics offer superior mechanical properties and heat resistance compared to thermoplastics. However, they are less commonly used in medical device manufacturing due to their irreversible curing process.
Design Considerations for Medical Device Plastic Molding
Complexity of the Part
The design of a medical device component plays a crucial role in determining the feasibility of plastic Molding. Parts with intricate geometries may require advanced Molding techniques or multiple manufacturing steps to achieve the desired results.
Material Selection
Choosing the right plastic material is essential for ensuring the functionality, durability, and biocompatibility of medical devices. Factors such as chemical resistance, sterilization compatibility, and regulatory compliance must be considered during the material selection process.
Regulatory Considerations in Medical Device Plastic Molding
FDA Regulations
The Food and Drug Administration (FDA) regulates the manufacturing and marketing of medical devices in the United States. Manufacturers must adhere to FDA guidelines for quality control, documentation, and reporting throughout the plastic Molding process.
ISO Standards
International Organization for Standardization (ISO) standards provide guidelines for quality management systems in medical device manufacturing. Compliance with ISO 13485 ensures that manufacturers meet stringent requirements for product safety and efficacy.
Advantages of Medical Device Plastic Molding
Versatility
Medical device plastic Molding offers unparalleled versatility in terms of design freedom and material selection. Manufacturers can create custom components tailored to specific medical applications with ease.
Speed of Production
The efficiency of plastic Molding processes allows for rapid production of medical device components, reducing time-to-market and meeting increasing demand for healthcare products.
Challenges in Medical Device Plastic Molding
Quality Control
Maintaining consistent quality standards is a significant challenge in medical device plastic Molding due to variations in material properties, Molding conditions, and process parameters.
Sterilization Concerns
Ensuring the sterility of plastic-moulded medical devices is critical for preventing infections and ensuring patient safety. Some plastic materials may not withstand standard sterilization methods, necessitating alternative approaches.
Future Trends in Medical Device Plastic Molding
Additive Manufacturing
The emergence of additive manufacturing technologies, such as 3D printing, presents exciting opportunities for innovation in medical device plastic Molding. These techniques enable the production of complex geometries and customized designs with enhanced speed and precision.
Biocompatible Materials
Advancements in material science are driving the development of biocompatible plastics tailored for medical device applications. These materials offer improved performance, durability, and compatibility with the human body.
Case Studies
Case Study 1: Custom Implant Manufacturing
Case Study 2: Disposable Medical Device Production
Conclusion
Medical device plastic Molding like Medical Injection Molding plays a crucial role in the production of high-quality, reliable components used in a wide range of medical applications. By leveraging advanced manufacturing techniques and innovative materials, manufacturers can meet the evolving needs of the healthcare industry while ensuring patient safety and satisfaction.