The One Step That Makes or Breaks Your Industrial Maintenance Routine
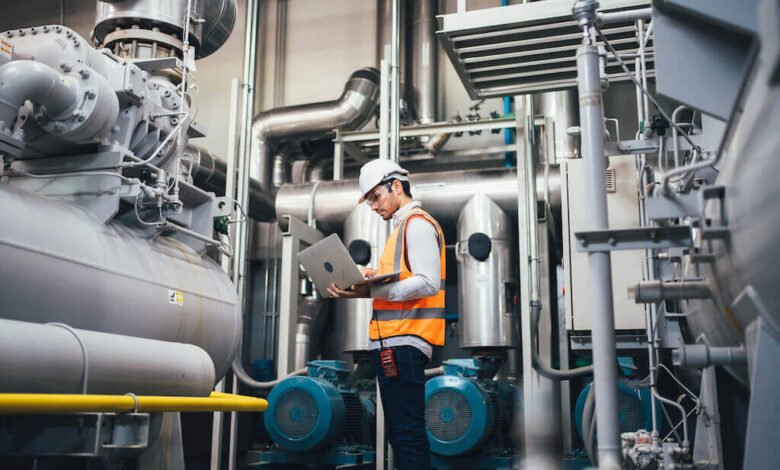
Industrial maintenance is often thought of as a checklist: change the filters, check the fluid levels, lubricate the joints. But if you’re still seeing premature wear and unexpected breakdowns even after following every standard procedure, you’re not alone. One overlooked step could be quietly sabotaging the entire system: how you prepare your surfaces before repair or refurbishment.
That preparation phase—especially when dealing with corrosion, heavy debris, or old coatings—can determine how well everything else holds up. Many facilities rely on a blast chamber for this step, as it provides a controlled environment for deep surface cleaning and ensures contaminants are fully removed before coatings or repairs begin.
But whether you’re using advanced equipment or manual techniques, what matters most is recognising surface prep as a core part of maintenance—not an afterthought.
Why Surface Contamination Undermines Everything
Contaminants like rust, oil, or old paint might seem like cosmetic issues, but they actually interfere with nearly every subsequent action—whether it’s painting, welding, sealing, or bonding. A clean-looking surface can still hide microscopic debris that prevents coatings from sticking or causes seals to break down early.
The result? You end up redoing jobs, facing premature failures, or wondering why expensive coatings didn’t last as promised.
See also: Precision Preservation: Mastering Quality and Safety with a High-Tech Food Dryer Machine
Spotting the Signs of Inadequate Prep
If your equipment keeps falling short of its projected service life, it might not be the fault of the parts or the materials—but the foundation they’re applied to. Red flags include:
- Blistering, peeling, or flaking coatings soon after application
- Surfaces that rust or corrode more quickly than expected
- Welds that crack or underperform
- Lubricants that appear ineffective despite regular application
In many cases, the root cause is poor surface cleanliness or uneven prep.
Maintenance Isn’t Just About Moving Parts
When people think of upkeep, they usually picture gears, engines, or belts. But structural components like tanks, piping, and panels need just as much attention—especially when exposed to heat, pressure, or moisture.
This means that non-mechanical surfaces shouldn’t be ignored. If a steel panel begins to pit or corrode, it can compromise insulation, safety barriers, or protective enclosures. Taking the time to inspect and clean these surfaces is just as essential as tuning up moving parts.
Make Surface Prep Part of the Workflow
Integrating cleaning and prep steps into your formal workflow doesn’t require a full overhaul. It just requires intention. Assign responsibility for it, document it, and give your team the tools and time to do it properly.
If you rely on third-party contractors or service teams, be sure they’re held to the same standards. A fresh coat of paint or a weld repair may look good in the short term, but its performance depends entirely on how well the surface was prepped first.
Extend the Life of Coatings and Repairs
Some of the most costly repairs in industrial settings come not from the initial damage—but from failed repairs. A valve housing that leaks again, a painted beam that rusts within a year, or a welded joint that splits under load all mean time, labour, and money wasted.
You can prevent most of that by investing just a bit more time upfront. Thorough surface cleaning doesn’t just reduce failure—it multiplies the effectiveness of every dollar you spend on coatings, labour, and replacement parts.
Balance Efficiency with Longevity
We all know time is money. But skipping prep to save a few hours can cost far more down the road. That said, not every job requires the same level of detail. Know when to go deep and when to go fast. For example:
- Critical load-bearing parts need full-scale cleaning and inspection.
- Visual-only components may only need basic treatment.
- High-pressure systems demand precision prep for sealing and bonding.
Use your maintenance records to identify which types of parts or locations experience the most premature failures. Chances are, those are also the ones that would benefit most from a renewed focus on surface prep.
A strong maintenance culture isn’t built on what tools you own—it’s built on what standards you set. The best teams know that success doesn’t always come from doing more work. Sometimes it comes from doing one crucial step better.
Whether you’re handling complex machinery or routine refurbishments, don’t underestimate the power of proper preparation. Over time, that one decision can define whether your maintenance program is consistently reactive—or reliably preventive.